Rational Commercial Combi Oven Servicing & Repairs in Birmingham
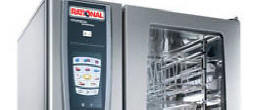
Tel: 01922 254044
Electrical & mechanical servicing and repairs of Rational Commercial Combi Ovens.
Electrical Equipment Repairs carry out routine
servicing and repairs to
Rational Commercial Combi Ovens.
Rational Commercial Combi Ovens are without
doubt the top choice of combi
oven for the catering
professional, and they deliver
fantastic results time after
time.
Regular cleaning is
absolutely key to these machines
running smoothly and
efficiently.
However, from
time to time, although you've
kept your side of the deal by
keeping it clean, they sometimes
go wrong.
Whether it's a
recurring error or service code,
or a component failure, we're
here to assist you.
There's never a good time for your Commercial Combi to go wrong, but being Commercial Trained & Certified, and using only genuine Commercial parts, we're here to get you back up and running with the minimum of fuss and disruption.
The problems we encounter are
numerous, there are many pumps,
valves and sensors that can
cause intermittent and permanent
faults.
Many faults are caused by a
sensor failure, or an electrical
or mechanical component failure
- some of the most common error
codes are
listed below;
Service Codes – SCC white Efficiency
- Service 10 >>Problem>> SC pump has high water level
- Service 11 >>Problem>> CDS sensor sending too many pulses
- Service 12 >>Problem>> CDS sensor without signal
- Service 13 >>Problem>> Steam generator isn't refilled during steam mode
- Service 14 >>Problem>> Level electrode isn't recognizing water
- Service 17 >>Problem>> SD card not initialized
- Service 18 >>Problem>> Defective SD card
- Service 19.1 >>Problem>> SD card not inserted
- Service 20.## >>Problem>> Defective thermocouple: (eg; Service 20.20.2)
- Service 23 >>Problem>> SSR steam short circuit
- Service 24 >>Problem>> SSR hot air short circuit
- Service 25 >>Problem>> Improper water flow during CleanJet
- Service 26 >>Problem>> Permanently closed drain valve
- Service 27 >>Problem>> Drain valve won't close during initialization
- Service 28 >>Problem>> Thermocouple steam generator B5 temperature is above 356 degrees F (180 degrees C)
- Service 29 >>Problem>> PCB temperature is above 185 degrees F (85 degrees C)
- Service 30 >>Problem>> Unit runs in emergency humidity control
- Service 31.## >>Problem>> Faulty core probe: (eg; Service 31.16)
- Service 32.0-1-2 >>Problem>> Faulty ignition box
- Service 33.1-2 >>Problem>> Faulty ignition box
- Service 34.# >>Problem>> Bus signal problems: (eg; Service 34.2)
- Service 35 >>Problem>> Bus signal can't be processed due to disconnected ultravent
- Service 36 >>Problem>> Defective differential pressure sensor P1
- Service 37 >>Problem>> Differential pressure sensor P1 isn't in expected range
- Service 40 >>Problem>> Care pump is broken or doesn't fill enough solution into the steam generator
- Service 41 >>Problem>> Defective solenoid valve Y3, blocked moistening valve or CDS isn't sending pulses
- Service 42 >>Problem>> Defective solenoid Y4 Care, hose to Care container blocked/kinked or CDS isn't sending pulses
- Service 43 >>Problem>> Solenoid Y1, Y3 or Y4 is passing water/won't close and CDS is always sending pulses
- Service 44 >>Problem>> Steam not heating during CleanJet+Care
- Service 60 >>Problem>> Incorrect initialization of ignition box
- Service 63 >>Problem>> Self-test running without water
- Service 100 >>Problem>> Defective SC pump or calcified level electrode
- Service 120 >>Problem>> Defective Care pump M12 or level electrode
Why not give us a call today to enquire about routine servicing or to book a service call?
Call us on 01922 254044 or visit our Contact page
An out of hours service is
also available for when things
just can't wait
Services Menu
Further Reading
Content will be posted here shortly.